Automation in US Manufacturing: Trends and Impact
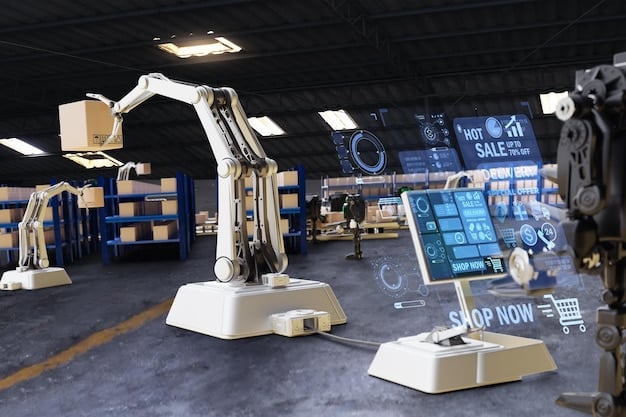
Automation is revolutionizing the US manufacturing sector, driving efficiency, productivity, and reshaping the workforce through innovative technologies and strategies.
The US manufacturing landscape is undergoing a massive transformation, and at the heart of this change is how automation is reshaping the US manufacturing landscape: a look at current trends. From robotics to artificial intelligence, automation technologies are being implemented to streamline operations, improve productivity, and enhance competitiveness in a global market. This article delves into the current trends, impacts, and future possibilities of automation in the US manufacturing sector.
The Rise of Robotics in US Manufacturing
Robotics has been a cornerstone of manufacturing automation for decades. However, recent advancements in technology have led to the development of more sophisticated and versatile robots, capable of performing a wider range of tasks. The integration of these robots is transforming how manufacturing processes are executed, offering numerous benefits and driving efficiency to new heights.
Advanced Robotics Technologies
Modern industrial robots are equipped with advanced sensors, AI-driven control systems, and improved dexterity. These features allow them to perform complex and precise tasks, such as welding, assembly, and material handling, with greater accuracy and speed. This increased capability makes them invaluable assets in a variety of manufacturing environments.
Collaborative Robots (Cobots)
Collaborative robots, or cobots, are designed to work alongside human employees, enhancing their productivity and safety. Unlike traditional industrial robots, cobots are equipped with safety features such as force-limiting sensors and obstacle detection, enabling them to operate in close proximity to humans without posing a risk. Cobots are particularly beneficial in tasks that require a combination of human dexterity and robotic precision.
- Enhanced Safety: Cobots are designed with advanced safety features to prevent injuries when working alongside humans.
- Increased Efficiency: By automating repetitive or physically demanding tasks, cobots free up human workers to focus on more complex and value-added activities.
- Improved Flexibility: Cobots can be easily reprogrammed and redeployed to different tasks, providing manufacturers with greater flexibility and adaptability.
- Reduced Costs: While the initial investment in cobots may be significant, the long-term benefits of increased productivity and reduced labor costs can lead to substantial savings.
The integration of robotics in US manufacturing is not just about replacing human workers with machines. It’s about creating a more efficient, safer, and more productive work environment where humans and robots can work together to achieve common goals.
AI and Machine Learning in Manufacturing
Artificial intelligence (AI) and machine learning (ML) are playing an increasingly important role in modern manufacturing. These technologies enable manufacturers to analyze vast amounts of data, optimize processes, and make more informed decisions. The application of AI and ML is transforming various aspects of manufacturing operations, from predictive maintenance to quality control.
Predictive Maintenance
One of the most promising applications of AI in manufacturing is predictive maintenance. By analyzing data from sensors and equipment, AI algorithms can predict when a machine is likely to fail, allowing manufacturers to perform maintenance before a breakdown occurs. This proactive approach reduces downtime, minimizes repair costs, and extends the lifespan of equipment.
Quality Control
AI-powered quality control systems can detect defects and anomalies in products with greater accuracy and speed than traditional methods. These systems use machine vision and other sensors to inspect products in real-time, identifying even the smallest imperfections. By automating the quality control process, manufacturers can ensure higher product quality and reduce the risk of recalls.
AI and ML are transforming manufacturing by enabling manufacturers to make data-driven decisions, optimize processes, and improve product quality. As these technologies continue to evolve, their impact on the US manufacturing landscape will only grow stronger.
The Internet of Things (IoT) in Manufacturing
The Internet of Things (IoT) is another key technology driving automation in US manufacturing. IoT devices, such as sensors, actuators, and connected machines, collect and transmit data that can be used to optimize processes, improve efficiency, and enhance decision-making. The integration of IoT is creating a more connected and data-driven manufacturing environment.
Connected Factories
Connected factories leverage IoT technology to create a network of interconnected machines, sensors, and systems. This network enables real-time monitoring and control of manufacturing processes, allowing manufacturers to identify and address potential issues quickly. By connecting different parts of the factory, IoT facilitates better communication, collaboration, and coordination.
Real-Time Monitoring and Analytics
IoT devices generate vast amounts of data that can be analyzed to gain insights into manufacturing performance. Real-time monitoring and analytics enable manufacturers to track key metrics, such as production output, equipment utilization, and energy consumption. This information can be used to optimize processes, identify bottlenecks, and improve overall efficiency.
- Improved Visibility: IoT provides manufacturers with real-time visibility into their operations, allowing them to track performance and identify potential issues quickly.
- Enhanced Efficiency: By optimizing processes and reducing downtime, IoT can help manufacturers improve efficiency and reduce costs.
- Better Decision-Making: The data generated by IoT devices can be used to make more informed decisions about production planning, maintenance scheduling, and resource allocation.
The Internet of Things is revolutionizing manufacturing by creating a more connected, data-driven, and efficient environment. As IoT technology continues to advance, its impact on the US manufacturing landscape will only grow stronger, enabling manufacturers to achieve new levels of performance and competitiveness.
The Impact on the Workforce
Automation is not only transforming manufacturing processes, but also having a significant impact on the workforce. As machines and robots take over more tasks, the demand for certain types of jobs is decreasing, while the demand for others is increasing. This shift is creating both challenges and opportunities for workers and employers. It’s crucial to understand how to adapt to these changes to ensure a smooth transition.
Job Displacement
One of the main concerns about automation is the potential for job displacement. As machines become more capable, they can perform tasks that were previously done by human workers, leading to job losses in certain industries and occupations. This is particularly true for repetitive and low-skilled tasks. However, automation can also create new jobs in areas such as robotics, AI, and data analytics.
Skills Gap
As automation changes the nature of work, there is a growing skills gap in the US manufacturing sector. Many workers lack the skills needed to operate and maintain advanced technologies, such as robots, AI systems, and IoT devices. To address this gap, manufacturers need to invest in training and development programs that equip workers with the skills they need to succeed in the new automated environment. Employers can partner with local community colleges and vocational schools to develop customized training programs. Additionally, apprenticeships and on-the-job training can provide valuable hands-on experience.
Adapting to the changing workforce dynamics requires a proactive approach. By investing in worker training, fostering collaboration between humans and machines, and promoting policies that support workers in transition, the US manufacturing industry can harness the benefits of automation while mitigating its potential negative impacts.
Government Initiatives and Support
The US government recognizes the importance of automation in maintaining the competitiveness of the manufacturing sector. Various initiatives and support programs have been put in place to encourage the adoption of automation technologies and address the challenges associated with workforce transition. These programs aim to facilitate the integration of automation, support workforce development, and promote innovation in manufacturing.
Funding and Grants
The government provides funding and grants to support manufacturers in adopting automation technologies. These programs help companies invest in new equipment, implement advanced technologies, and train their workforce. For example, the Manufacturing Extension Partnership (MEP) program provides technical assistance and resources to small and medium-sized manufacturers. The MEP National Network can help manufacturers assess their technology needs, identify potential funding opportunities, and implement automation solutions.
Workforce Development Programs
To address the skills gap, the government has launched workforce development programs that provide training and education to workers in the manufacturing sector. These programs help workers acquire the skills they need to operate and maintain advanced technologies. The Workforce Innovation and Opportunity Act (WIOA) supports a range of training and education programs, including apprenticeships, on-the-job training, and classroom-based instruction.
Government initiatives and support play a critical role in facilitating the adoption of automation technologies and addressing the challenges associated with workforce transition. By providing funding, technical assistance, and workforce development programs, the government can help manufacturers embrace automation and remain competitive in the global economy. Collaboration between government, industry, and educational institutions is essential to ensure that the US manufacturing workforce is prepared for the future of work.
The Future of Automation in US Manufacturing
The future of automation in US manufacturing holds immense potential. As technology continues to advance, automation will become even more sophisticated, versatile, and integrated into all aspects of manufacturing operations. This includes the integration of advanced technologies like 3D printing, which allows for rapid prototyping and customized manufacturing, driving further innovation.
Emerging Technologies
Several emerging technologies are poised to revolutionize manufacturing automation, including artificial intelligence, augmented reality, and advanced robotics. AI will enable machines to learn, adapt, and make decisions autonomously. Augmented reality will provide workers with real-time information and guidance, enhancing their productivity and safety. Advanced robotics will enable machines to perform even more complex and delicate tasks.
Smart Manufacturing
The concept of smart manufacturing envisions a fully integrated and automated manufacturing environment where machines, systems, and people are seamlessly connected. In a smart factory, data is collected, analyzed, and used to optimize every aspect of the manufacturing process. This includes process optimization, predictive maintenance, and automated quality control.
- Increased Efficiency: Smart manufacturing can significantly improve efficiency by optimizing processes, reducing waste, and minimizing downtime.
- Improved Quality: By automating quality control inspections and monitoring production processes in real-time, manufacturers can ensure higher product quality and reduce the risk of defects.
- Enhanced Flexibility: Smart manufacturing enables manufacturers to respond quickly to changing market demands and customize products to meet specific customer needs.
The future of automation in US manufacturing is bright, with endless possibilities for innovation and improvement. By embracing emerging technologies, fostering collaboration, and investing in workforce development, the US manufacturing industry can harness the full potential of automation and lead the way in the global economy. As automation technologies continue to evolve, manufacturers must remain adaptable and proactive to stay ahead of the curve and achieve sustainable growth.
Key Point | Brief Description |
---|---|
🤖 Rise of Robotics | Advanced robots enhance manufacturing efficiency and precision. |
🧠 AI & ML | AI-driven systems optimize maintenance and quality control. |
🌐 IoT Integration | IoT connects factories for real-time monitoring and analytics. |
🧑🏭 Workforce Impact | Automation shifts job roles, requiring updated worker skills. |
FAQ
▼
The primary driver is the need to enhance efficiency, reduce costs, and improve competitiveness in a global market by adopting innovative technologies.
▼
Cobots are designed to work alongside humans, with safety features like force-limiting sensors, while traditional robots typically operate in isolated environments.
▼
AI algorithms analyze sensor data to predict when machinery is likely to fail, enabling proactive maintenance and reducing downtime.
▼
IoT devices facilitate real-time monitoring and control of processes, allowing manufacturers to optimize operations and improve decision-making.
▼
Smart manufacturing involves fully integrating and automating facilities with connected machines, improving optimization, quality, and flexibility across operations.
Conclusion
As automation reshapes the US manufacturing landscape, embracing these changes is crucial for sustained competitiveness. By leveraging robotics, AI, IoT, and supportive government initiatives, the US can enhance its manufacturing capabilities and secure a leading position in the global economy.