Robotics Revolution: Will Robots Take 40% of US Manufacturing Jobs by 2030?
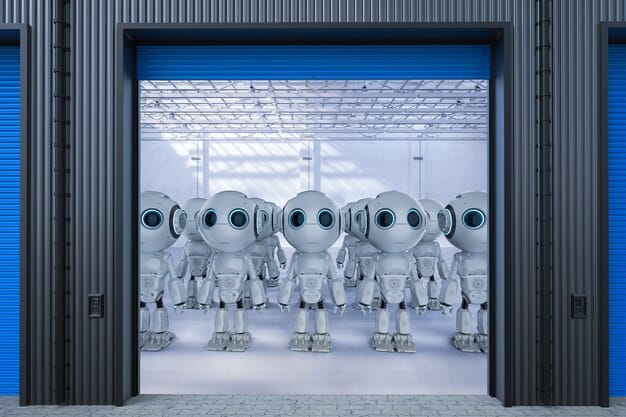
The Evolution of Robotics: Will Advanced Robots Automate 40% of US Manufacturing Jobs by 2030? explores the transformative impact of robotics in the US manufacturing sector, analyzing the potential for widespread automation, its economic implications, and the future of human labor in the industry.
The future of manufacturing is rapidly changing, driven by advancements in robotics and artificial intelligence. The pivotal question is: The Evolution of Robotics: Will Advanced Robots Automate 40% of US Manufacturing Jobs by 2030?
The Rise of Industrial Robotics
Industrial robotics has come a long way, evolving from simple automated arms to sophisticated systems capable of performing complex tasks. This evolution is fueled by advancements in AI, sensor technology, and materials science, making robots more adaptable and efficient.
The initial wave of industrial robots primarily focused on repetitive and dangerous tasks, such as welding and painting. However, modern robots are now capable of handling more intricate operations, including assembly, quality control, and even customization.
Key advancements in robotics
Several technological breakthroughs are driving the capabilities and adoption of industrial robots:
- AI-powered robots: AI algorithms enable robots to learn from experience, adapt to changing conditions, and make autonomous decisions.
- Advanced sensors: Enhanced sensors allow robots to perceive their environment with greater accuracy, improving their ability to perform complex tasks.
- Collaborative robots (cobots): Cobots are designed to work alongside humans, sharing workspace and tasks, enhancing productivity and safety.
The increasing sophistication of industrial robots is making them more attractive to manufacturers seeking to improve efficiency, reduce costs, and enhance product quality. As technology continues to advance, the potential for robotics in manufacturing will only expand.
The Current State of Automation in US Manufacturing
Automation is already prevalent in many US manufacturing sectors, but the extent of its adoption varies significantly across industries. Some sectors, like automotive and electronics, have embraced robotics extensively, while others lag due to factors such as cost and complexity.
Currently, the US manufacturing industry employs around 12 million people. While automation has been increasing, human workers still play a critical role in many processes. The question is how quickly and extensively robots will replace these workers in the coming years.
Sectors leading in automation
Certain industries are at the forefront of adopting robotics and automation:
- Automotive: Robots perform tasks such as welding, painting, and assembly in automotive manufacturing plants.
- Electronics: Robotics is essential for the precise assembly of electronic components.
- Food and beverage: Automated systems handle packaging, sorting, and quality control in food processing facilities.
The adoption of automation in these sectors has led to increased productivity, reduced error rates, and improved worker safety. Other industries are now looking to these leaders for best practices and strategies for implementing robotics.
Predicting the 40% Automation Threshold by 2030
Forecasting the future impact of robotics on US manufacturing jobs requires careful analysis of current trends, technological advancements, and economic factors. While predicting a specific percentage like 40% is challenging, several factors suggest that significant automation is likely.
The pace of technological innovation is accelerating, with new robotics solutions emerging at an unprecedented rate. This rapid development, combined with the increasing affordability of robots, makes it more likely that manufacturers will invest in automation.
Factors supporting increased automation
Several trends support the forecast of increased automation in US manufacturing:
- Advancing technology: Continued improvements in AI, sensors, and robotics hardware are making robots more capable.
- Cost reduction: The cost of robots is decreasing, making them more accessible to smaller manufacturers.
- Labor shortages: A shortage of skilled workers in manufacturing is driving companies to seek automation solutions.
While the 40% figure is an estimate, the overall trend indicates that automation will play an increasingly significant role in US manufacturing. The key is to understand the implications of this shift and prepare for the changes it will bring.
Economic Implications of Widespread Automation
The widespread automation of US manufacturing jobs will have profound economic implications, affecting employment, productivity, and the overall competitiveness of the industry. Understanding these effects is crucial for developing policies that support workers and promote economic growth.
One of the primary concerns is the potential displacement of human workers by robots. While automation can increase productivity and reduce costs, it can also lead to job losses, particularly for workers in routine, repetitive roles.
Potential economic effects
Automation can impact the US economy in several important ways:
- Job displacement: Automation may lead to job losses for workers in routine manufacturing roles.
- Increased productivity: Robots can work faster and more efficiently than humans, increasing overall productivity.
- Enhanced competitiveness: Automation can help US manufacturers compete more effectively in the global market.
To mitigate the negative impacts of automation, it is essential to invest in education and training programs that help workers develop skills needed for new jobs in the changing economy. Additionally, policies that support workers who are displaced by automation can help ensure a more equitable distribution of the benefits of technological progress.
The Future of Human Labor in Automated Manufacturing
Despite the rise of robots, human workers will continue to play a vital role in manufacturing. The key is to focus on tasks that require uniquely human skills, such as creativity, problem-solving, and critical thinking. The future of work in manufacturing will likely involve humans and robots working together in collaborative environments.
As automation takes over routine tasks, human workers can focus on higher-value activities, such as design, engineering, and management. This shift requires a workforce with the skills and knowledge to work with advanced technologies.
Roles for humans in automated manufacturing
Humans will continue to be essential in manufacturing in the following areas:
- Design and engineering: Developing new products and designing manufacturing processes.
- Maintenance and repair: Maintaining and repairing robotic systems.
- Management and supervision: Overseeing automated processes and ensuring quality control.
To prepare for this future, it is crucial to invest in education and training programs that focus on STEM skills (science, technology, engineering, and mathematics). These programs can help workers develop the skills needed to work effectively in automated manufacturing environments.
Strategies for Adapting to the Robotics Revolution
Adapting to the increasing automation of US manufacturing requires a proactive approach from businesses, governments, and individuals. By investing in education, training, and supportive policies, it is possible to harness the benefits of robotics while mitigating its potential negative impacts.
Businesses should invest in training programs that help their employees develop skills needed to work with robots. Governments can support this effort by providing funding for education and training initiatives, as well as policies that promote innovation and economic growth.
Key strategies for adaptation
To adapt to the robotics revolution, consider the following suggestions:
- Invest in education and training: Provide workers with the skills they need to work with robots.
- Support innovation: Promote the development of new technologies.
- Develop supportive policies: Implement policies that help workers who are displaced by automation.
By embracing these strategies, the US can ensure that the benefits of robotics are shared broadly, leading to a more prosperous and equitable future for all. Adaptation is crucial for maintaining a competitive edge and ensuring that the workforce is prepared for the changing landscape of manufacturing.
Key Point | Brief Description |
---|---|
🤖 Automation Growth | Robotics is rapidly expanding in US manufacturing, driven by tech advances and cost reductions. |
💼 Job Displacement | Increased automation may lead to job losses, particularly in routine manufacturing roles. |
🚀 Productivity Boost | Automation can significantly increase productivity and efficiency in manufacturing processes. |
📚 Skill Adaptation | Focus on STEM education and training to prepare workers for future roles in automated environments. |
Frequently Asked Questions
Automation is expanding rapidly, driven by technology advancements and cost reductions. Industries such as automotive and electronics are leading the way, with others catching up.
The automotive and electronics industries are leading in automation, implementing robotics for assembly, quality control, and various manufacturing needs. Food and beverage are also prominent.
Automation can lead to job displacement in routine tasks. However, humans will still be crucial in design, engineering, maintenance, and management roles within manufacturing.
Workers can adapt by focusing on skills that robots cannot replicate, such as problem-solving, creativity, and critical thinking. STEM education plays a vital role in preparing workers.
Investing in training programs, supporting tech innovation, and implementing policies that support workers displaced by automation are key strategies for successful adaptation.
Conclusion
The evolution of robotics and its potential to automate a significant portion of US manufacturing jobs by 2030 presents both challenges and opportunities. While concerns about job displacement are valid, proactive strategies such as investing in education and training, supporting innovation, and developing supportive policies can help ensure a smooth transition. By embracing these changes, the US can harness the benefits of robotics to enhance productivity, competitiveness, and overall economic prosperity.